El Grupo BMW continúa avanzando hacia una economía circular más eficiente, reutilizando residuos plásticos y piezas usadas para fabricar nuevos componentes mediante tecnología de impresión 3D. A través de procesos innovadores, el polvo sobrante de impresión y piezas descartadas se convierten en filamentos y gránulos reciclados, que son reutilizados en dispositivos auxiliares, herramientas de producción y otras aplicaciones clave.
Esta tecnología se desarrolla en el Campus de Fabricación Aditiva en Oberschleißheim, donde cada año se reciclan hasta 12 toneladas de polvo para crear nuevos materiales de impresión. Estos se distribuyen a distintas plantas del Grupo BMW en todo el mundo, fomentando una producción más flexible, rápida y sustentable.
El proyecto comenzó en 2018 con la iniciativa “bottleUP”, que buscaba reutilizar botellas PET para impresión 3D. Desde entonces, el equipo liderado por Paul Victor Osswald ha logrado desarrollar componentes robustos a partir de materiales reciclados, consolidando un sistema que hoy abastece a múltiples plantas de producción de BMW a nivel global.
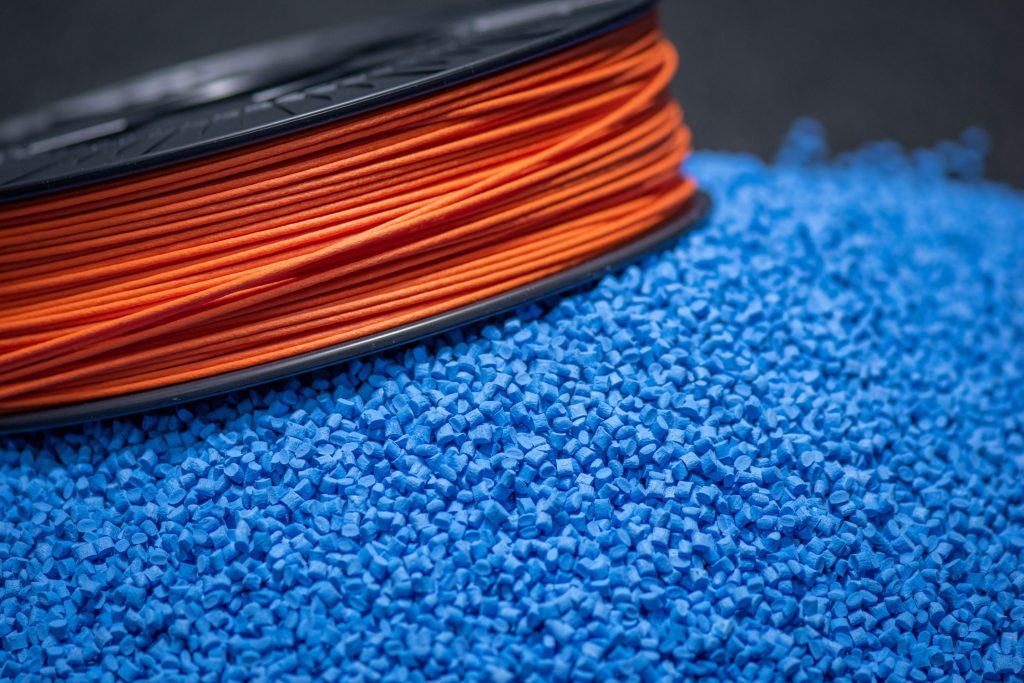
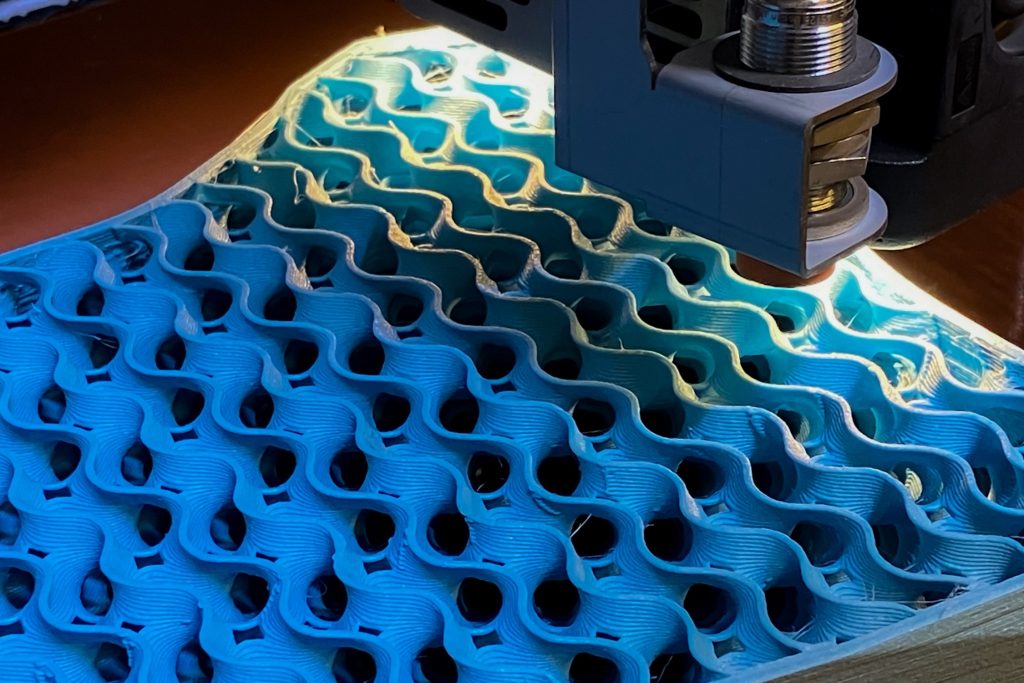
Además del beneficio medioambiental, esta innovación ha permitido mejorar la eficiencia en las líneas de producción, reducir costos y optimizar la ergonomía para los colaboradores. El Campus ofrece un paquete completo que incluye filamento reciclado, parámetros de impresión validados y capacitación técnica para todas las plantas, garantizando resultados de alta calidad y una implementación ágil.
Actualmente, cada planta del Grupo BMW cuenta con al menos una impresora 3D. Estas se utilizan para fabricar desde fijaciones y herramientas hasta componentes que protegen piezas delicadas durante el ensamblaje. Por ejemplo:
- En la planta de Múnich, se imprime un componente que asegura temporalmente la barra de dirección durante su instalación en el vehículo.
- En la planta de BMW Motorrad en Berlín, se usan soportes impresos en 3D para aplicar decoraciones en los paneles de las motocicletas.
- En Dingolfing, se desarrolló un soporte magnético para tornillos que facilita el trabajo con destornilladores inalámbricos, evitando pérdidas durante el ensamble.
Este enfoque no solo reduce tiempos de respuesta, sino que también potencia la creatividad de los equipos técnicos para resolver desafíos del día a día.
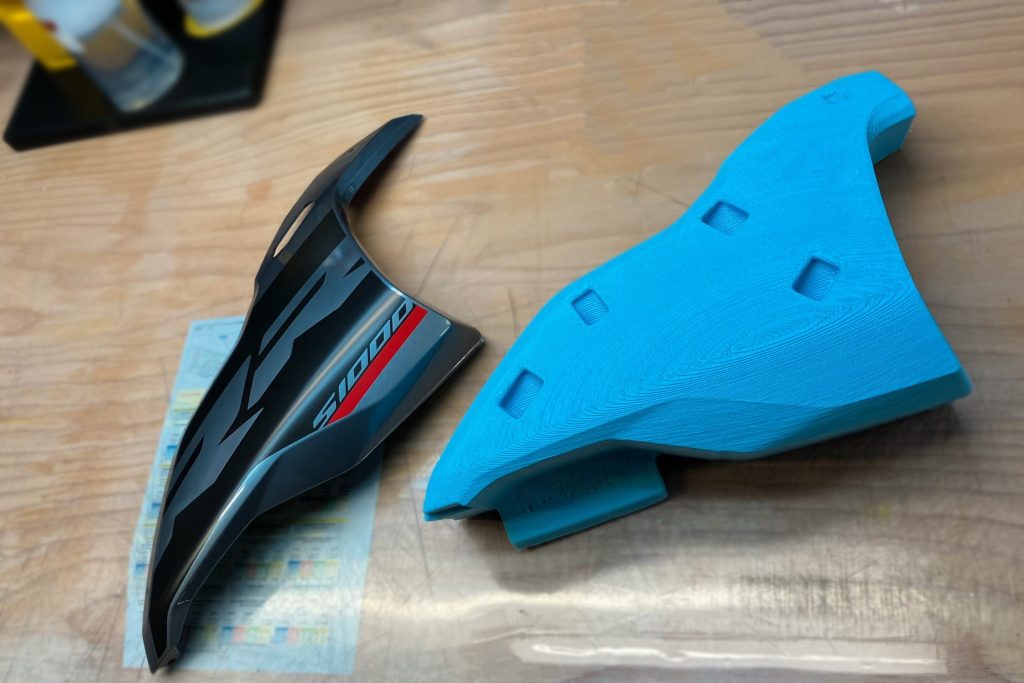
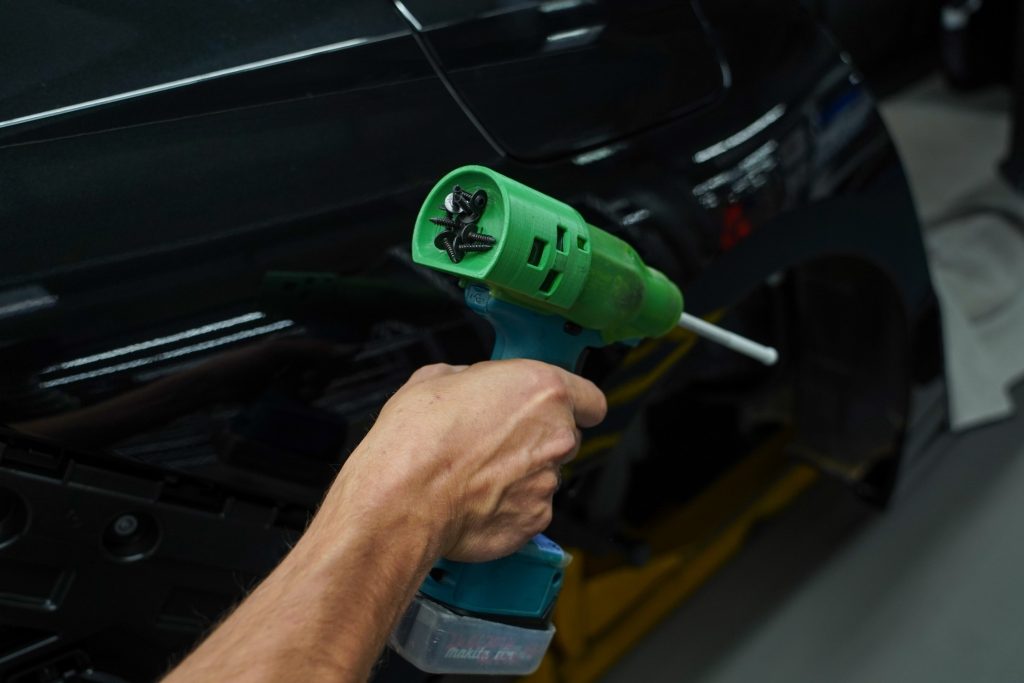
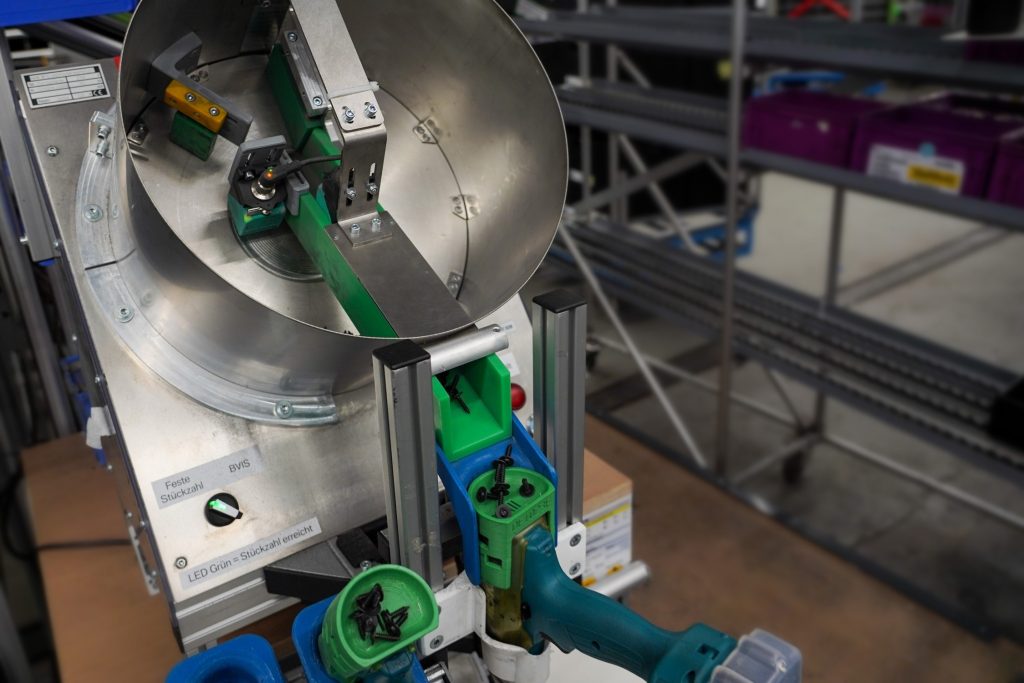
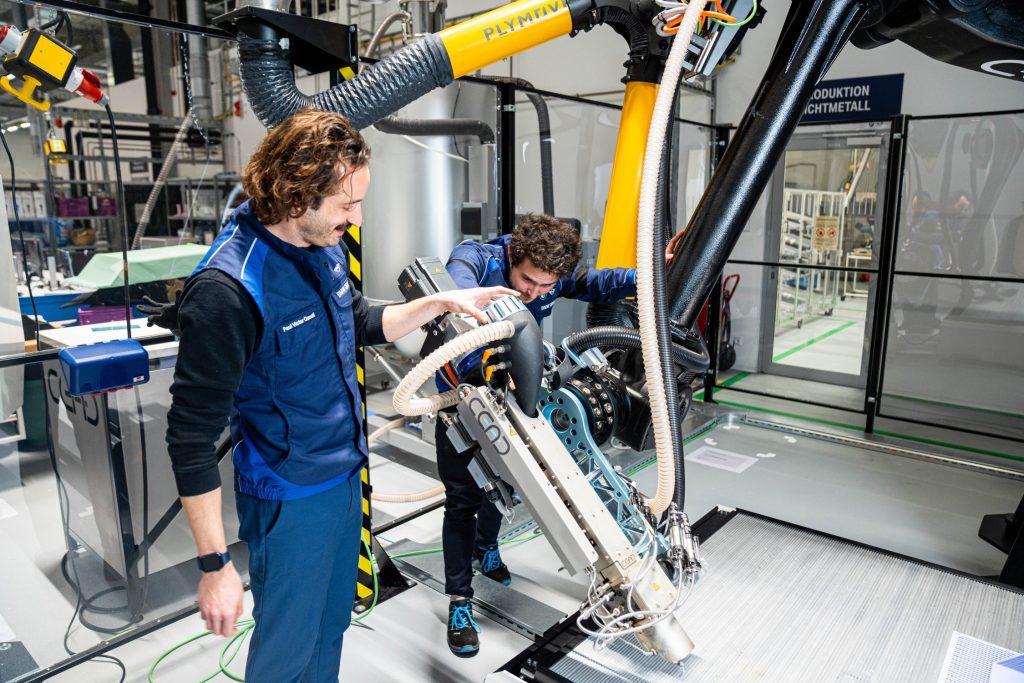